1. Ván khuôn
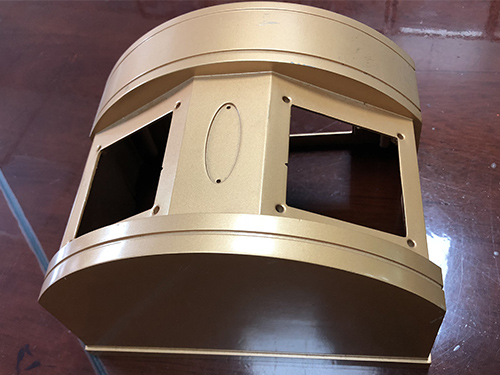
1. Bề mặt bên ngoài yêu cầu phải sáng và phẳng. Hai lỗ đục lỗ được thêm vào khung khuôn phía trước và phía sau. Chú ý những nơi không có vật chèn để tránh các bộ phận rơi ra ngoài.
2. Khung khuôn tấm AB khớp với nhau tạo thành 0,1-0,15, đồng thời bổ sung thêm một vách ngăn nước bay để ngăn nhôm bay ra ngoài gây thương tích cho người.
3. Để tránh mẫu bị biến dạng, ít nhất phải tạo hai cột đỡ, một trên nón song song và một trên nón song song. Hãy cẩn thận để không can thiệp vào các bộ phận khác.
4. Khuôn thêm 2-4 dấu ngoặc ở giữa và dấu ngoặc ở giữa, và mặt khung ở giữa tốt nhất nên được làm có giới hạn.
5. Tấm đáy của khuôn phải mở để thuận tiện cho việc tản nhiệt.
6. Nên cắt bốn góc của khuôn để tránh va vào cột xanh trong quá trình lắp đặt.
7. Bàn lỗ bên trong của vòng định vị cần được thấm nitơ sau khi mài bên trong và đánh bóng dọc theo hướng phóng.
8. Chiều dài từ đáy vòng làm mát trên bề mặt vòng định vị đến bề mặt của nón chia thường bằng độ dày của bánh. Có 2 cách để sửa vòng làm mát này là hàn và gia nhiệt và ép.
9. Nón shunt phải được làm mát bằng cách vận chuyển nước và cách bề mặt của nón shunt 25-30mm.
10. Bốn lỗ trụ dẫn hướng của đế khuôn phải là các rãnh cạy có độ sâu 8-10mm.
11. Đế khuôn phải được tôi và tôi luyện, tốt nhất là đế khuôn rèn.
12. Để thuận tiện cho việc tháo các phần chèn của khuôn bên trong, có thể thêm một lỗ trên bề mặt của khuôn, sau đó có thể thu thập một số ốc vít không đầu để thuận tiện cho việc tháo rời và thay thế các phần chèn.
13. Các lỗ nâng phải sâu ít nhất M30 và 45, và ít nhất 2 lỗ ở trên cùng.
14. Súng cao su bên ngoài phải được trang bị vỏ bảo vệ lò xo để tránh lò xo bị biến dạng.
15. Bề mặt cao hơn bề mặt đế khuôn và cần tiếp xúc với mặt đất nên bổ sung thêm các cột đỡ.
2. Khuôn trong, khuôn chèn
1. Thực hiện xử lý giảm căng thẳng trước khi xử lý nhiệt sau khi xử lý. Tôi hợp kim nhôm thông thường HRC45+/-1°C, tôi hợp kim kẽm HRC46+/-1-1°C
2. Dung sai vừa vặn của khuôn bên trong: Thông thường, nó phải nhỏ hơn khung khuôn khoảng 0,05-0,08mm và có thể dễ dàng lấy ra và đưa vào khung khuôn bằng vòng nâng.
Dung sai vừa vặn của thimble: độ hở của thimble lớn hơn hoặc bằng 8 mm là 0,05mm,
Khe hở thimble nhỏ hơn hoặc bằng 6mm là 0,025mm.
3. Tất cả các góc vuông và góc nhọn trên khuôn trong phải lớn hơn R0,5mm.
4. Sử dụng vít lưỡi phẳng để chặn các lỗ thừa trên bề mặt khuôn bên trong.
3. Thiết kế hệ thống xả xỉ và chạy xỉ
1. Đường dẫn dòng chảy chính của bánh vải trên nón shunt phải nằm trong khoảng 1/3 diện tích bề mặt của hình tròn. Bằng cách này, bề mặt phân khuôn được đóng lại trước khi vật liệu lạnh nhanh chóng đi vào khoang đúc.
2. Rãnh chính phía trên hình nón xẻ phải được làm thành hình chữ “W”, độ dày của bánh phải là 15-20mm.
3. Nói chung, chiều dài của đường dẫn chính phải là 30-35mm và khuôn phải là 5-10° ở một bên.
4. Nói chung, kênh dòng chảy ngang tốt nhất nên uốn cong và thực hiện nhiều hơn 2 bước để ngăn vật liệu lạnh xâm nhập vào khoang qua kênh dòng chảy ngang, dẫn đến tạo thành các đường chắn lạnh trên bề mặt sản phẩm.
5. Nói chung, tốt nhất nên thêm 2 bộ đệm ở vị trí cổng nơi kênh dòng chảy chéo đi vào sản phẩm, để vật liệu lạnh bị chặn hoàn toàn ra khỏi khoang.
6. Nói chung, mức độ của ống lót dưới ống dẫn chính phải được đúc và phải cao hơn R2.
7. Phải tránh lõi nhô ra ở phía đối diện của đường dẫn chính, đồng thời túi xỉ ở phía đối diện của đường dẫn chính phải là rác trước, sau đó tùy theo tình huống mà mở ra.
8. Túi đựng xỉ tốt nhất nên sử dụng mặt phẳng của sân, mặt cắt ngang hình bán nguyệt, rãnh nước vào và rãnh xả cách nhau 1/3. Đầu vào nước của túi xỉ cũng nên được bỏ qua.
9. Khe xả phải được giảm giá và chuyển tiếp trơn tru, tuân theo các quy tắc của "3.2.1".
10. Để thuận tiện cho việc chế biến, nên bỏ qua cổng ở điểm nối của kênh dòng chảy trực tiếp và sản phẩm, không dễ bị thất thoát thịt trong quá trình xử lý sau.
4. Cơ cấu kéo lõi
1. Thanh trượt phải có ít nhất một lỗ khuôn treo ở mặt trên và mặt dưới để thuận tiện cho việc tháo lắp.
2. Đáy thanh trượt phải là máng cắt, dải chịu mài mòn phải làm thành 2 miếng cao hơn bề mặt đế khuôn dưới 8-12mm để thuận tiện cho việc làm sạch xỉ nhôm trong quá trình sản xuất.
3. Hạt của thanh trượt phải là rãnh chịu mài mòn, góc 45° với hướng kéo lõi
4. Cơ cấu trượt phải linh hoạt trong việc dẫn hướng và trượt, ổn định trong chuyển động, có khe hở 0,08--0,12MM.
5. Sau khi đóng khuôn, thanh trượt và khối khóa phải được ép chặt, diện tích tiếp xúc không nhỏ hơn 2/3 và có ứng suất trước nhất định.
If you'd like to speak to a member of the Anebon team for Aluminum Casting,CNC Machined Custom Service,CNC Turning Alloy, please get in touch at info@anebon.com
Thời gian đăng: Feb-25-2021